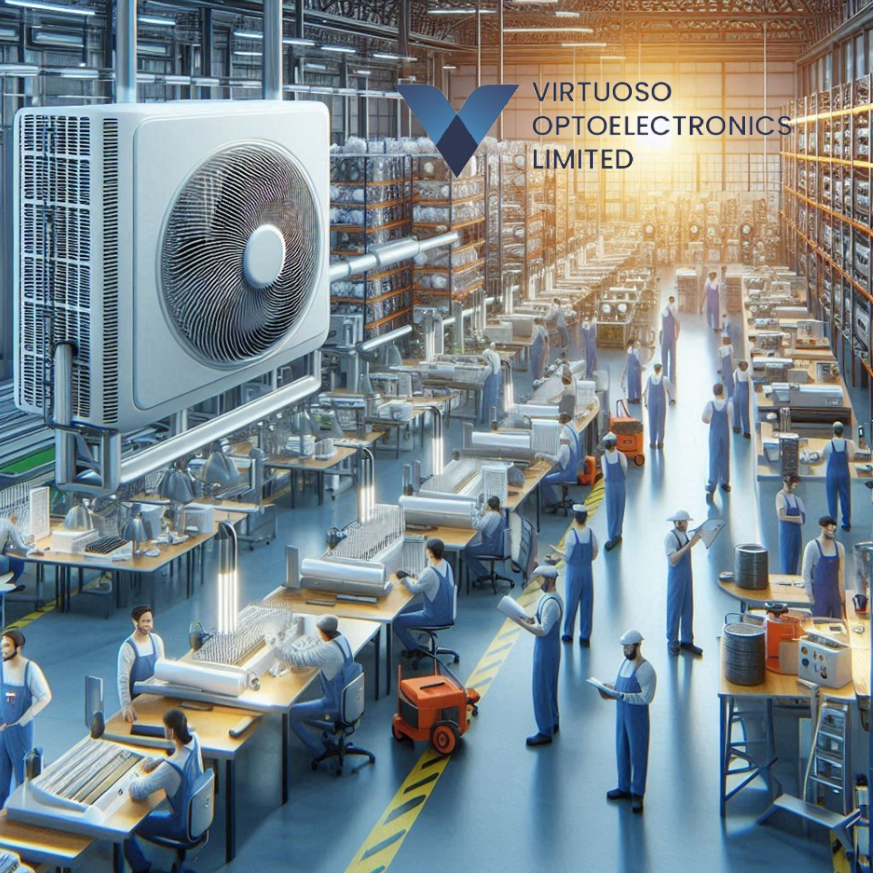
Recently, we visited multiple manufacturing facilities of Virtuoso Optoelectronics Ltd. Below are our learnings from the plant visit and management discussion.
Yeah, the heat just got real!
This summer has been one of the hottest ever, not just in India but across Asia, with multiple countries experiencing insanely high temperatures!
Northern and Western India have seen the mercury soar above 50 degrees Celsius. Delhiites know this all too well, having faced an all-time high of 52.3 degrees Celsius.
For those in Western India, we’ve all seen those viral videos of BSF soldiers cooking papad and eggs on the scorching desert sand in Rajasthan. In Ahmedabad, water sprinklers have been installed at traffic signals just to offer a bit of relief from the blistering heat.
This time, even the people of Bengaluru couldn’t brag about their usually pleasant weather, as they recently faced a sweltering 38.5 degrees Celsius.
So yeah, this summer was crazy hot. What an understatement, right?
The Effect
This scorching heat has driven a surge in consumer products made to help people stay cool. This season, fans, coolers, refrigerators, and especially air conditioners have flown off the shelves.
ACs, in particular, have been a hot commodity, with the industry selling 1.0 crore units in FY24. Projections suggest this could climb to 1.2 crore units in FY25, largely due to the relentless summer heat. Depending on the monsoon, these numbers might even rise further. Many manufacturers are already concerned they might not be able to keep up with the skyrocketing demand.
Speaking of ACs, let’s talk about the largest AC company in India, Voltas Ltd. In FY24, Voltas sold an impressive 0.2 crore units, making it a significant beneficiary of the ongoing heatwave.
This brings us to our learning for today. As part of our research, we visited the manufacturing plants of Virtuoso Optoelectronics Ltd., a contract manufacturer that makes 80% of its revenue from manufacturing ACs for its clients, with Voltas as its key customer. Such visits provide us with a direct glimpse into how companies operate. So without much ado, let’s unpack the AC manufacturing process, step-by-step.
Basics Of AC Manufacturing
It is common knowledge that an AC consists of two main components: a sleek, smart-looking Indoor Unit that enhances the aesthetics of your room or office, and a bulky, less attractive Outdoor Unit that sits outside on the balcony or window, out of sight. Both components are manufactured separately. Let’s take a look at how they are made at Virtuoso’s manufacturing plants.
Outdoor Unit (ODU) Manufacturing Process: 3-Step Process

Step 1: Manufacturing ODU Chassis
The process begins with manufacturing metal parts from metal sheets. The machines to manufacture these parts can be sourced from India, but the moulds have to be pre-dominantly imported from China.
- Punching & Welding – Metal sheets undergo moulding and punching to create various structures of the ODU chassis. These structures are then welded together to create specific parts.
- Pre-treatment – ODU parts can either be made using galvanized or cold-rolled sheets. Parts made using cold-rolled sheets are prone to rusting and, therefore, require anti-corrosion treatment. But, before that, substances like oil, rust, and chemicals are removed using a washing treatment.
- Corrosion Treatment – The pressed parts are then dipped in a specific liquid and heated at a defined temperature for 10-15 mins. Afterwards, they are rinsed in water for 1 min.
- Painting – Treated parts are then manually loaded onto a conveyor, where each part is painted using automatic guns that sprinkle powder. If the painting machine misses any parts, a technician manually covers them with a paint gun.
Step 2: Assembling internal parts in the ODU
Here, all the internal components, i.e. compressor, copper coil, motors, fans, and PCB, are fitted in the ODU.
- Clients Provide – Voltas provides compressors, motors, and PCBs.
- Virtuoso Made – Virtuoso makes coils (copper pipes), and fans in-house.
- Finishing Touch – After assembling, the ODU is complete with all its components. The company then proceeds with the remaining steps: first, they vacuum clean the units, fill them with gas, and test for gas leaks. The company conducts gas leak tests four times to ensure there are no leaks.
- Adding Labels – After that, the necessary stickers, as per the client to whom the product is going to be shipped, are attached to the ODUs.
Step 3: Testing
Yes, after the initial gas testing, the company further tests the finished ODUs. They are stored for 24 hours and then tested again for gas leaks.
Once that’s done, the ODUs are finally ready to be picked up by the clients.
As of FY24, Virtuoso has an installed capacity capable of manufacturing 400,000 ODUs per year.
Phew! This completes the outdoor unit part of the story. Now, let’s move on to the indoor unit story. Let’s go!
Indoor Unit (IDU) Manufacturing Process: 6-Step Process

Step 1: Manufacturing IDU Chassis
Again, the chassis are manufactured first. Here, the injection moulding process is used to create the exterior of the IDU. If you are confused, we are talking about the plastic body of the IDU.
Step 2: Heat Exchanger Assembly
- The heat exchanger, specifically the evaporator coils, is made from aluminum or copper tubes.
- The tubes are tested for leaks. Once they pass the tests, they are welded together to create heat exchanger. This is how a Heat Exchanger looks like.

Step 3: Component Assembly
- Now, fans, motors, and heat exchangers are assembled and go into the chassis of the IDU.
- After that, the control box is installed in the IDU. It includes PCBs (again, provided by Voltas, while Virtuoso’s own PCB is currently in the R&D stage).
- Finally, the circuits, including the display for showing the AC temperature, etc, are fixed on the head of the IDU.
Step 4: Testing
- At this stage, necessary testing is conducted to ensure electrical safety and effective signal reception from the remote.
- After that, the IDU assembly is complete.
Step 5: Final Assembly & Coding
- Here, the rest of the accessories, like the remote, warranty card, user manual, etc., are added.
- Again, based on the customer, the required labels are attached to the IDU.
- Afterwards, the product is scanned by a computer, and the final product code and serial numbers are recorded.
Step 6: Packaging & Shipment
- At this point, the IDUs are packaged according to the clients’ specifications.
- Finally, after completing all the steps, the products are shipped to the clients.
Currently, Virtuoso has an installed capacity to manufacture 800,000 IDUs per year.
Manufacturing Facilities
The company has 3 main plants for assembling ODUs and IDUs which are supported 3 feeder plants that carry out the process of moulding & carbon fiber felt (CFF), Copper tubing, Die Casting, brass components, etc.
Currently, Virtuoso relies on Voltas for 65-70% of its sales. The company aims to reduce this dependency to 50% by expanding into the commercial refrigerator market.
Future of Virtuoso:
- The company is building a new plant to manufacture commercial refrigerators, which will be piloted by August. The initial capacity will be 150,000 units, which will be ramped up to 400,000 units within the next two years.
- In the coming years, Virtuoso expects to earn ~₹200-400 cr from this new venture, with an EBITDA margin of 12-15%.
If you are still here, CONGRATULATIONS, you are now aware of the AC manufacturing process.
Useful Fact: ACs are eligible for government assistance under the PLI scheme. Additionally, Virtuoso is eligible for and has already received the first tranche of PLI incentives. According to the company, most of these benefits will be passed through.
So Yeah, that sums up our insights from the plant visit Virtuoso. We hope you enjoyed reading about it as much as we enjoyed bringing it to you. We’ll continue to share such unique experiences whenever we get the chance, so stay tuned!
Until next time, happy investing!
Fin Meme of the Week
