Insights from the Plant Visit and Management meet

This week on LEARNING OF THE WEEK, we’re sharing some insights from our recent plant visits and management meet with India’s only listed elevator company.
India is rising, both literally and figuratively. As cities expand and skylines evolve, elevators have become more than just a convenience; they are a necessity. Rapid urbanization has made India the second-largest elevator market in the world, just behind China.
Despite the scale of this industry, there isn’t a single publicly listed elevator company in India. Major players like KONE, Schindler, and OTIS are all privately owned. This is largely due to the industry’s niche nature, high capital requirements, and reliance on long-term contracts, making private ownership the preferred model.
However, there is one exception.
Aaron Industries Ltd.

Aaron isn’t a traditional elevator manufacturer. You won’t find “Aaron” branded elevators in buildings because the company doesn’t install elevators directly. Instead, Aaron operates as an OEM, specializing in elevator components. It produces cabins, doors, and other elevator components, supplying them to both leading elevator brands and regional players. While the leading brands account for 30-35% of India’s elevator market, regional players capture the rest by competing on cost and offering greater customization.
In our discussion with the management, we learned that installing an elevator for a 10-floor building costs around Rs. 13-14 lakh with a regional player, while branded players charge Rs. 17-18 lakh. This price gap gives regional players a competitive edge, particularly in cost-sensitive markets.
Aaron serves both segments, providing standardized as well as decorative elevator components. Its B2B business model allows it to partner with leading elevator companies rather than compete with them, enabling scalable growth without entering the highly regulated installation business.
What goes into Elevators?
An elevator consists of multiple components, including:
- Cabins (where passengers stand)
- Doors (installed on every floor and inside the elevator)
- Shafts, motors, and control panels (for movement and operation)
- Other electrical and mechanical parts
Most of these components are made from stainless steel (SS) due to its strength, durability, and resistance to corrosion. It also offers a sleek, modern look, making it a preferred choice for elevators.
However, a significant portion of India’s stainless steel demand is met through imports, primarily from China and Vietnam, which supply large volumes at competitive prices. The dependence on imports is even higher for designer or decorative SS sheets, which are used in high-end elevator cabins and doors.
While Aaron’s primary business is manufacturing elevator components, it has also backward integrated into SS processing to reduce reliance on imports and offer high-quality processed and decorative SS sheets. This integration expands its capabilities beyond just elevator manufacturing, enabling the company to meet both the demand for elevator parts and quality SS materials.
Business Divisions:
- Elevator Division – Manufacturing elevator cabins, doors, and other components.
- Stainless Steel Processing Division – Processing and supplying decorative SS sheets for elevators and other industries
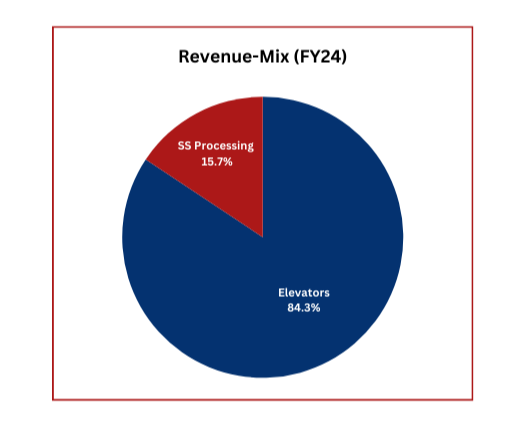
Elevator Division: Aaron’s Core Strength
The company primarily manufactures elevator doors and cabins, which together account for a major portion of elevator costs. While a building may have only one cabin per elevator, it requires multiple doors—one for each floor. This makes doors a recurring and significant cost in elevator installations.
Aaron specializes in:
- Standardized products (plain SS doors and cabins)
- Decorative or Custom designs (decorative SS finishes based on client requirements)
Aaron’s products contribute 35-40% of the total elevator cost, making it a key player in elevator value-chain.
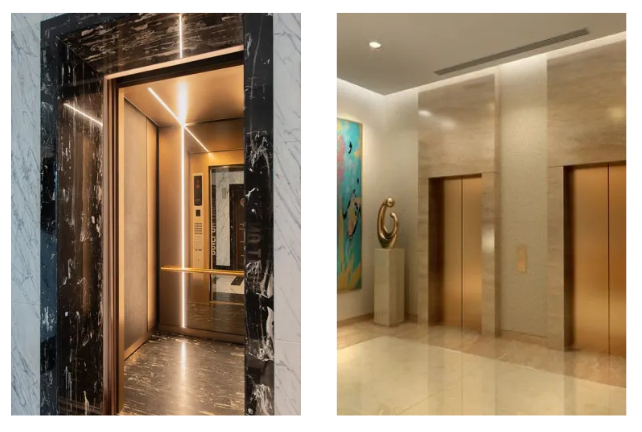
Production Process
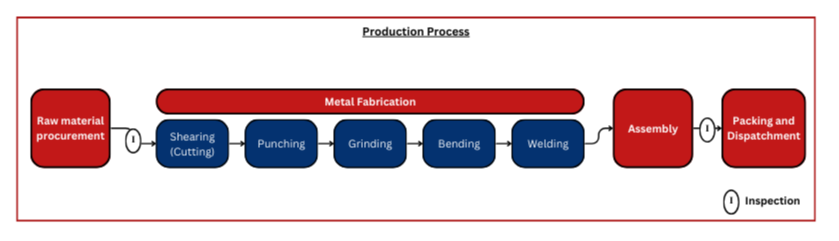
Raw material procurement: The company sources stainless steel (SS 304) sheets or coils from domestic suppliers or imports from Vietnam and other countries when needed in bulk. These sheets undergo a quality check to ensure strength, durability, and defect-free material.
Metal fabrication: The raw metal sheets are transformed into elevator doors and cabin components through a series of precise processes:
- Shearing (Cutting): Large sheets are cut into smaller, precise pieces using cutting machines.
- Punching: Machines create holes and cutouts for screws, bolts, and air vents, ensuring easy assembly.
- Grinding: Sharp edges are smoothed out for safety and a refined finish
- Bending: Sheets are shaped into walls, doors, and panels using controlled pressure.
- Welding: Key parts like door frames and cabin walls are permanently joined to ensure strength and durability.
- Assembly: Each component undergoes a quality check to verify its shape, size, and finish. Any defects are corrected before moving forward. The fabricated parts are then assembled into complete elevator cabins and doors, with reinforcements added for structural integrity
- Packing and Dispatchment: A final inspection ensures the correct size, fit, smooth finish, and strong welded joints. Defective products are either sent for rework or rejected. Approved products are carefully packed and dispatched for delivery.
Key Elevator Products
A large part of Aaron’s production focuses on automatic elevator doors, available in various sizes, designs, and configurations for residential, commercial, industrial, and car lifts. The company also manufactures elevator cabins ranging from 3-passenger to 30-passenger capacity, widely used in residential and commercial projects. One of Aaron’s key strengths is its decorative cabin designs, offering extensive customization options that few companies in India provide. In addition to doors and cabins, Aaron supplies various supporting components essential for complete elevator installations.
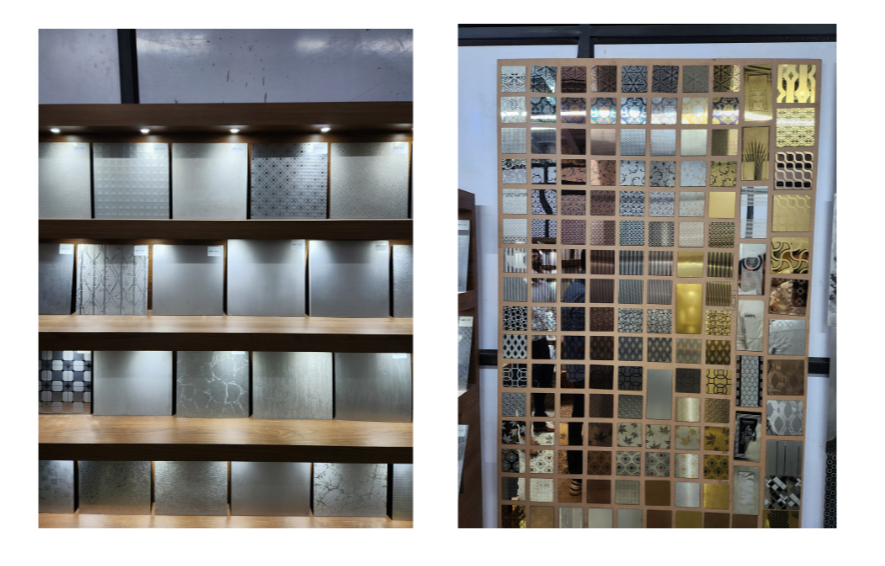
Stainless Steel Processing Division:
In this division, Aaron specializes in processing SS sheets with various finishes, ranging from basic brushed or matte textures to decorative color-coated (PVD) designs. By offering a wide selection of SS sheet finishes, including custom jobs, the company helps bridge the domestic demand that was previously met through imports.
These processed sheets are primarily used in elevator doors and cabins but also find applications in interior decor, modular kitchens, and other design-focused industries.
Finishes & Processes Offered:
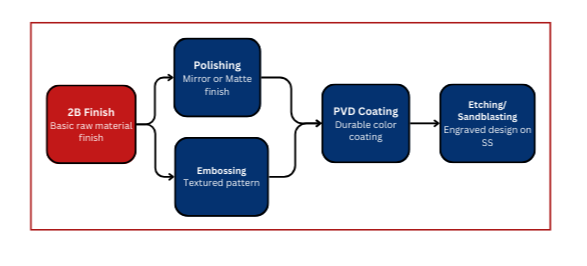
Manufacturing Expansion
Aaron operates two manufacturing units in Gujarat—one in Udhana and a newer, more advanced facility in Kosamba, which the company expanded into after going public in FY18. While the Udhana unit focuses on cabin manufacturing, the Kosamba facility is a larger setup that also handles polishing, door mechanics, and other key processes.
During our visit to the Kosamba unit, we got a firsthand look at a well-equipped factory handling everything from manufacturing and processing to designing, finishing, and assembly, all under one roof. A key highlight was the Salvagnini S4+P4 line, an advanced Italian fabrication system, along with a specialized embossing line, both part of Aaron’s recent expansion.
The Salvagnini system automates punching, cutting, and bending of sheet metal, improving efficiency and precision in production. Meanwhile, the embossing line gives Aaron the capability to offer a wider variety of stainless steel designs, a feature that remains limited among domestic player
With these upgrades, Aaron has expanded its manufacturing capacity from 2,000 doors and 200 cabins per year to 4,000 doors and 400 cabins annually, enhancing its production capabilities.

Additional Insights
As an OEM, Aaron faces fewer certification and compliance requirements than elevator installers. However, its components are designed to meet industry safety standards, ensuring seamless integration for its clients. Additionally, management shared that Aaron serves over 650 customers and maintains a strong ~80% retention rate, driven by its precision in auto door systems, technical expertise, premium quality, and diverse design offerings.
Conclusion
India’s elevator industry is growing, driven by rapid urbanization, high-rise construction, the need for vertical expansion in space-constrained cities, and a rising demand for premium designs. While global brands dominate installations, regional players are gaining traction by offering cost-effective and customized solutions. Companies like Aaron stand to benefit from the industry’s shift toward domestic manufacturing and reduced import reliance, creating new opportunities across the elevator value chain.
We hope this virtual journey of Aaron’s plant visit have given you deeper insights into the business and the industry.
Happy Investing!!!
Disclaimer: These insights are based on our observations and interpretations, which might not be complete or accurate. Bastion Research and its associates do not have any stake in companies mentioned. This newsletter is for educational purposes only and is not intended to provide any kind of investment advice. Please conduct your own research and consult your financial advisor before making any investment decisions based on the information shared in this newsletter.
MEME OF THE WEEK
